Find out how plastic extrusion boosts production efficiency
Find out how plastic extrusion boosts production efficiency
Blog Article
Trick Advantages and Factors To Consider of Carrying Out Plastic Extrusion in Your Jobs
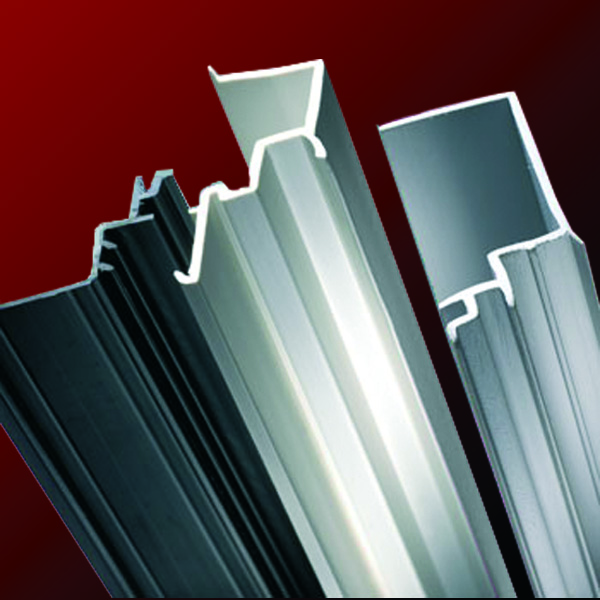
Recognizing the Essentials of Plastic Extrusion
Plastic extrusion, a staple in the production industry, is a process that involves melting raw plastic material and reshaping it right into a continual profile. This profile, when cooled down, can be cut into desired sizes or curled for later use. The elegance of plastic extrusion depends on its adaptability. A vast array of items, from piping to window frames, can be generated. The process requires an extruder, an intricate equipment with a warmed barrel, a turning screw, and a die at the end. The plastic product, in the form of pellets, is fed right into the extruder, where it's melted and forced through the die, taking its shape. The choice of plastic and the layout of the die figure out the item's attributes.
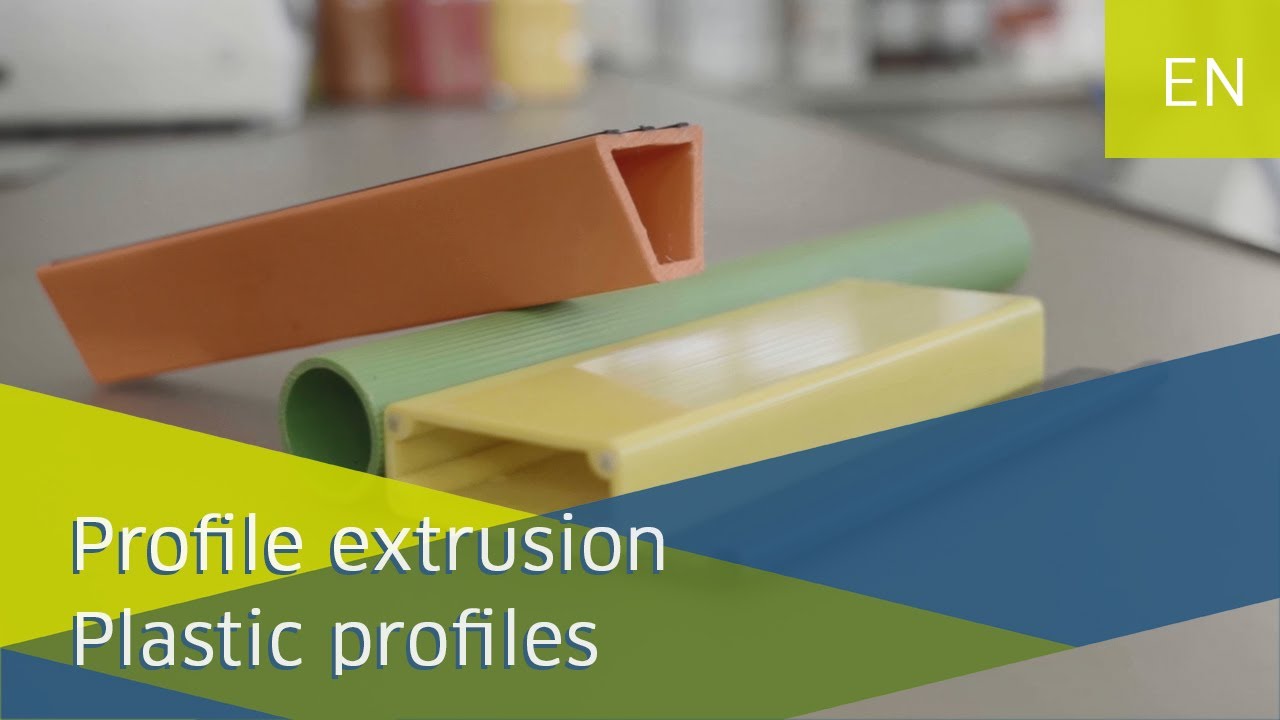
The Economic Advantage of Plastic Extrusion
The financial benefit of plastic extrusion lies mostly in two locations: cost-effective product manufacturing and valuable production speeds. With plastic extrusion, businesses can create high quantities of material at a lower price compared to various other approaches. Moreover, the procedure flaunts a remarkable manufacturing speed, substantially minimizing time and additional improving its financial viability.
Cost-Effective Product Manufacturing
A significant advantage of plastic extrusion is its impressive cost-effectiveness. In addition, the extrusion process enables for a high degree of precision in forming the plastic, lowering the demand for pricey post-production changes or modifications. All these factors make plastic extrusion a highly economical choice for many projects, offering an attractive equilibrium in between expense and efficiency.
Beneficial Production Speeds
While keeping the cost-effectiveness of the materials, an additional notable benefit of plastic extrusion hinges on its rapid production speeds. This efficiency in the manufacturing procedure is attributed to the continuous nature of the extrusion procedure, enabling high-volume production in a fairly brief time span. The rate of manufacturing directly associates to a decrease in labor expenses and a rise in result, thereby enhancing the general economic practicality of the procedure. Moreover, the hectic production does not compromise the quality of the last item, ensuring regular and trustworthy outcomes. This mix of high quality, speed, and cost-effectiveness emphasizes the considerable financial advantage of implementing plastic extrusion in various tasks.
Flexibility and Customization: The Strengths of Plastic Extrusion
Among the popular staminas of plastic extrusion hinges on its flexibility and customization potential. These qualities unlock to unrestricted layout opportunities, giving suppliers the capacity to customize products to specific needs. This heightened level of personalization not just improves item capability but additionally dramatically enhances item individuality.
Unlimited Layout Possibilities
Plastic extrusion beams in its capacity to provide virtually infinite style possibilities. This technique offers freedom to develop complex profiles and complex shapes, a feat hard to attain with other fabrication strategies. Owing to the fluid nature of liquified plastic, the process is adaptable enough to yield a varied variety of measurements, forms, and dimensions. The plastic can be controlled to match unique specs, permitting the manufacturing of tailored geometries and meeting specific customer demands. Plastic extrusion can take care of a selection of plastic kinds, expanding its application range. This adaptable method, therefore, offers a vast array of industries from building to automotive, product packaging to electronic devices, and beyond. With plastic extrusion, the design opportunities are essentially countless.
Boosting Product Uniqueness
The adaptability of plastic extrusion can considerably improve product individuality. This process allows developers to explore different shapes, sizes, and colors, providing the flexibility to produce distinct products right here that attract attention in the marketplace. It is this modification that lends a distinct identification to every product, identifying it from its rivals.
In addition to its visual advantages, the customizability of plastic extrusion likewise provides sensible benefits. Therefore, plastic extrusion not just increases product originality yet additionally its utility and marketability.
Design Limitations in Plastic Extrusion: What You Required to Know
Exactly how can create limitations possibly impact the process of plastic extrusion? While plastic extrusion is functional, style constraints can curtail advice its benefits. Certain facility layouts might not be feasible due to the restrictions of the extrusion process, possibly limiting the creation of complex accounts. The procedure is much less suitable for multi-chambered or hollow frameworks. Additionally, the extrusion procedure might not constantly provide the desired surface area coating, especially for those calling for high gloss or optical quality. Material option can also present challenges, as not all polymers are ideal for extrusion. High-temperature resistant plastics, for circumstances, might present difficulties. Understanding these restraints is important for efficient implementation of plastic extrusion in your projects. plastic extrusion.
Reviewing the Environmental Impact of Plastic Extrusion
While recognizing design constraints is a considerable aspect of plastic extrusion, it is similarly vital to consider its ecological implications. The procedure of plastic extrusion entails melting plastic products, potentially releasing harmful gases right into the atmosphere. Using recycled plastic materials in the extrusion procedure can minimize ecological effect.
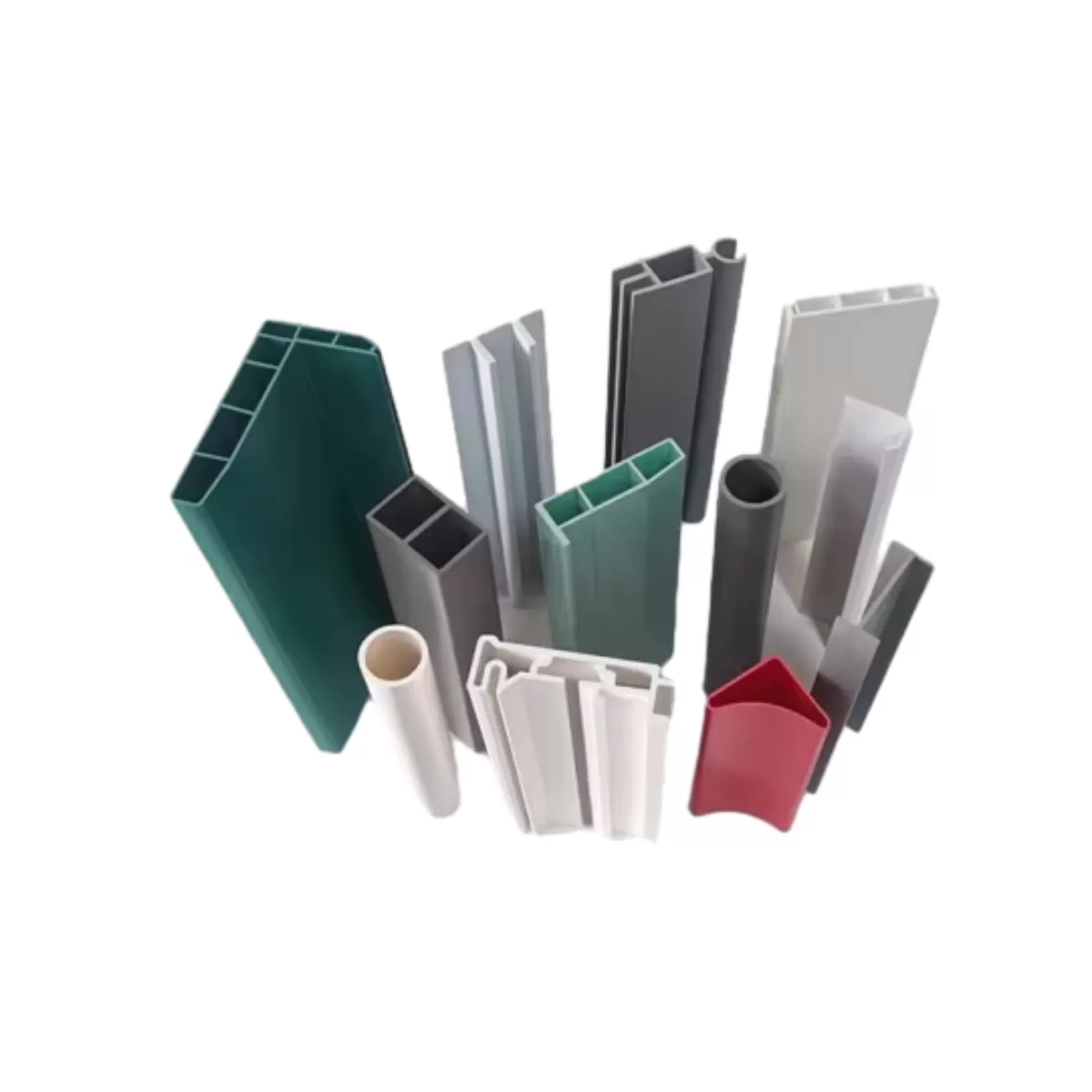
Situation Research Study: Effective Projects Making Use Of Plastic Extrusion
Success tales in the field of plastic extrusion are plentiful, showing both the convenience and efficiency of this manufacturing procedure. One significant example is the creation of PVC pipelines used in contemporary pipes. This procedure entails melting plastic and forming it into a continual tube, providing significant cost and sturdiness benefits. Another effective instance is the manufacturing of plastic movie for packaging and farming. With extrusion, producers can create extremely personalized, slim, and robust films. Automotive industries additionally profit, making use of extruded plastic for parts like trim or seals, enhancing vehicle durability. These circumstances highlight plastic extrusion's vital role in different sectors, vouching for its versatility, cost-effectiveness, and reputable result.
Final thought
In verdict, plastic extrusion uses a effective and affordable technique for generating intricate shapes with marginal waste. Including plastic extrusion into projects can lead to successful outcomes, as evidenced by many instance research studies.
Plastic extrusion, a staple in the production market, is a procedure that includes melting raw plastic material and improving it useful site into a continuous profile. Plastic extrusion can deal with a selection of plastic kinds, broadening its application extent.Just how can make limitations potentially affect the process of plastic extrusion? The procedure of plastic extrusion involves melting plastic materials, possibly releasing unsafe gases into the setting. Using recycled plastic materials in the extrusion procedure can decrease environmental impact.
Report this page